Our Analytical capabilities enable us to characterize the Polymer properties produced in our Miniplants.
PRT GmbH offers a variety of polymer analysis. Please contact us for your specific needs. The flexibillity and experience within PRT GmbH will assist you in obtaining your desired results. Our integrated aproach comprises all the essential elements of catalytic and free-radical polymerization technologies.
Particle size distribution
Particle size distribution can be analysed by laser diffraction
Alternatively, sieve analysis can be done
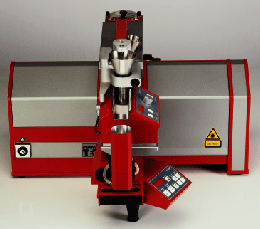
Melt Flow Index
For industrial standardization the melt flow index (MFI), melt flow rate (MFR), melt volume rate (MVR), and melt density/viscosity can be analysed with the Davenport Melt Flow Indexer MFI-10.
The method complies with BS 2782 Part 7: Method 720A, ISO 1133 and ASTM 1238 Methods A and B
Temperature range: | 40 – 400 °C |
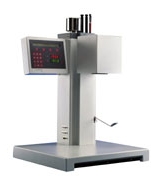
Molecular weight
The molecular weight can be analysed using Lauda Intrinsic viscosity analysis.
The molecular weight can be determined using the Mark-Houwink relationship. With inhouse developed techniques, the intrinsic viscosity (Staudinger Index) can be evaluated up to viiscosity average molecular weights of 7×106 g/mol in case of UHMWP
PRT can convert intrinsic viscosity data to moleczlar weight for PE and PP especially
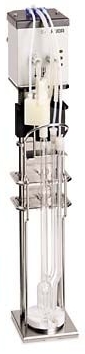
Porosity
We can do pore size analysis of particles using a Micromeretics Autopore III 9410 mercury porosimeter.
Pore Size range: | 0.006~360 µm |
Pressure Range: | 0 – 4081 Bar |
Intrusion Resolution: | < 0.1 µl/g |
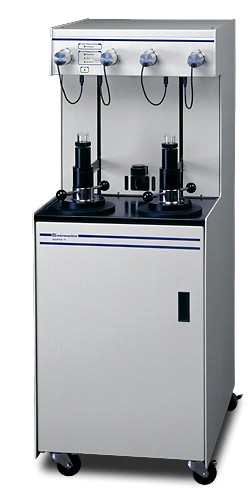
Differential Scanning Calorimetry (DSC)
Crystallinity and melting point of polymers can be analyzed
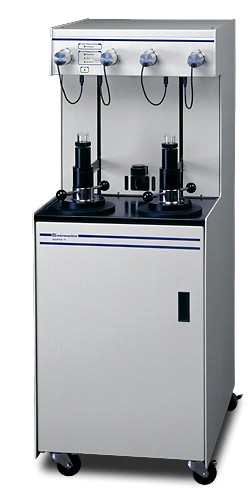
Strain-Stress Analysis
Prepared specimen can be analzed; alternatively:PRT can prepare specimen from powders by sinter-pressing
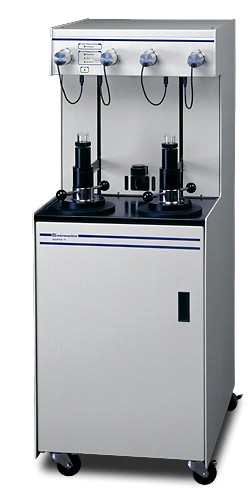